Résine epoxy thermo-conductrice
En combinant des résines exclusives Cotronics® et des durcisseurs spécialement chargés, nous avons obtenu la conductivité électrique requise pour certaines applications. Ces colles adhèrent au verre, aux céramiques, aux métaux et aux plastiques. Elles présentent une excellente résistance aux agents chimiques et aux solvants courants.
Les couches conductrices de chaleur que permettent ces produits peuvent servir en électronique, pour fixer les transistors, les radiateurs et les refroidisseurs, les éléments photovoltaïques, les bases de montage en céramiques, etc.
-
Duralco® 128 : Chargée en céramique, elle présente une grande résistance diélectrique. Elle polymérise à température ambiante et résiste à 260 °C.
-
Duralco® 132 : Chargée à l'aluminium, elle forme un excellent échangeur thermique. Elle polymérise à température ambiante et résiste à une température de 260°C.
-
Duralco® 133 : Chargée également d'aluminium, elle dispose de la meilleure résine Cotronics organique. Elle résiste à une température de 315°C avec un recuit préalable à 180°C.
-
Duralco® 134 : C’est une graisse conductrice de la chaleur non-durcissable, isolante électriquement pouvant s'installer en couches entre composants et radiateurs. Sa consistance permet de la remplacer facilement.
-
Duralco® 135 : Similaire à la Duralco® 134, la charge de céramique est remplacée par une fine poudre d'aluminium qui améliore les qualités de transfert thermique.
Données techniques des adhésifs époxy électro-conducteurs
Conseils pour la mise en œuvre des résines époxy haute température.
Les époxydes Cotronics® en général
Ces produits spéciaux haute performance sont spécifiés et fabriqués suivant des méthodes communes dérivées de principes généraux qui induisent leurs ressemblances ; ils se distinguent les uns des autres par :
- Leur nombre de composants (1 ou 2)
- Leur «charge» additionnelle éventuelle
- Leur polymérisation, à température ambiante ou par chauffage préalable (pouvant aller jusqu'à 120°C)
Un peu de chimie
Les résines époxydes sont des mélanges de produits organiques, oligomères pour la plupart, contenant plus d'un groupement époxyde par molécule. Dans les produits Cotronics®, Duralco® et Durapot®, on met en œuvre la résine Novalac ; celle-ci est durcie par les réactions de condensation en milieu acide (ce qui les catalyse) entre radicaux phénol ou crésol d'une part et formaldéhyde d'autre part.
Comme durcisseur, on utilise :
- Des amines, pour les systèmes polymérisant à température ambiante
- Des anhydrides acides, pour des systèmes polymérisant à température plus élevée
- Le complexe aminé BF3, pour des systèmes à un seul composant
Lors du durcissement chimique, les réactions de polymérisation produisent un composé rendu infusible et insoluble par sa structure moléculaire tridimensionnelle.
Comme ces réactions se comportent de manière stœchiométrique, le respect des proportions exactes de mélange est essentiel pour la qualité du résultat.
L'utilisation en parallèle de «charges» permet de faire varier certains comportements, comme la conductivité thermique ou électrique, ou bien la résistance mécanique. Une charge comme l'argent (Duralco® 118, 120, 124) permet des assemblages conduisant l'électricité, alors qu'une charge d'oxyde d'aluminium (Duralco® 4400, 4700) donne des collages conduisant la chaleur, mais se comportant comme des isolants électriques.
Mono- et Bi- composant
Les résines à deux composants ont une meilleure conservation à température ambiante ; elles montrent de meilleures qualités mécaniques en général et offrent une grande variété de propriétés thermiques et autres paramètres physiques.
Le principal avantage d'un système à un seul composant est d'éviter la préparation d'un mélange en proportions précises ; à contrario leur consistance (viscosité, thixotropie) varie lentement lors du stockage à température ambiante.
On peut en principe mélanger un produit bi-composant dès la fabrication, mais il faut alors le porter tout de suite à -40°C. On obtient ainsi une colle mono-composant qui doit être stockée à -40°C. La conservation d'un tel produit dans ces conditions atteint un an.
Temps de pottage
On désigne par ce terme le temps pendant lequel il est possible de travailler le mélange d'un produit bi-composant (ou de faire dégeler un produit mono-composant) sans risquer d'altérer le processus de sa mise en œuvre.
Dans le cas d'une colle mono-composant, temps de pottage et temps de stockage sont semblables. Au début de cette durée, on observe pour certaines résines une lente évaporation, qui entraîne, elle aussi, une légère variation de la viscosité et de la thixotropie. On considère le temps de pottage, écoulé, lorsque la résine ne peut plus être utilisée (dosée, pesée...) sans dommage.
Les techniques de préparation et les applications influent aussi sur les possibilités d'usage d'une résine à sa viscosité optimale. Ainsi le temps de pottage ne dépend pas seulement de la résine et de sa composition, mais également des techniques utilisées pour son utilisation. La façon dont un matériau donné sera travaillé (resp. stocké) pourra faire varier le temps de pottage (à température ambiante) entre un jour et une semaine. II faut donc considérer les temps de pottage indiqués comme des valeurs de référence. Noter aussi que dans cet intervalle la viscosité des produits peut doubler. Dans la plupart des procédés de mise en œuvre ce doublement peut être tolérable sans problème.
Les temps de pottage à température ambiante des produits bi-composants s'échelonnent de quelques minutes à une semaine ou plus. Un refroidissement particulier n'est pourtant pas recommandé, car il n'apporte aucun avantage et car les composants risquent de cristalliser.
Nettoyage
Le nettoyage des outils tachés de résine non polymérisée se fait avec :
- De l'acétone
- Du MEC (Methyl-Ethyl-Cétone)
Pour les taches polymérisées, la chaleur, la force mécanique, ou un produit dissolvant les époxydes (ex. le dichlorométhane) en viendront à bout.
Propriété des surfaces
Les surfaces d'application doivent être exemptes de déchets, de poussières, d'huiles ou de reste de solvants. Pour assurer un collage optimal.
Cycle de polymérisation, durcissement
Le cycle de durcissement est un ensemble de paliers de température que doit suivre une résine pour une bonne polymérisation. Plusieurs combinaisons de paliers de température sont disponibles pour chaque produit, les rendant utilisables dans des applications variées.
De même on aura un ensemble de paliers pour chaque type de préparation envisageable (chauffage à l’air, four ventilé, plaque chauffante, etc…). En principe, un chauffage court à haute température assure le durcissement complet et donne la meilleure résistance à l’eau, aux gaz et autres fluides. Pour les résines conductrices (de l’électricité ou de la chaleur) ces mêmes procédures permettent d’obtenir les plus faibles résistances possibles.
Mais bien sûr dans tous les cas cette température élevée rend les résines plus cassantes.
Une polymérisation utilisant des températures plus basses et des temps de chauffage plus longs ne donnera pas à la résine des caractéristiques physiques, électriques ou thermiques les plus élevées ; mais, en revanche, elle restera plus souple, et encaissera mieux les tensions thermomécaniques variables entraînées par les dilatations des matériaux qu’elle assemble.
Les paliers temps/température indiqués dans les spécifications des produits d’assemblage doivent donc être considérés plutôt comme des propositions que comme des références impératives. Des variations dans les conditions de chauffage conduisent à des changements de propriétés du produit polymérisé. Les conditions optimales du durcissement dépendent de l’application envisagée et leur découverte reste empirique.
Une technique, excellente mais longue, consiste à procéder à un durcissement gradué. On obtient d’excellents résultats, même en première approche, en l’utilisant telle qu’elle est décrite sur les emballages et quelle que soit l’application visée. Ce processus proposé sur l’emballage représente le meilleur premier essai possible. Dans de nombreuses applications industrielles, les paliers de polymérisation proposés pourront sans doute être considérablement réduits.
N.B. : On ne peut jamais trop faire durcir !
Comme le lien entre durée et température de durcissement est de nature exponentielle, on se souviendra de la règle suivante : aux alentours de 100°C, une baisse de température de 10°C double le temps de polymérisation nécessaire pour obtenir un résultat identique, alors qu’une augmentation de 10°C le divise par deux.
Domaines de température
Les résines époxydes et polyamides sont des mélanges organiques qui se décomposent et s’évaporent à haute température.
Dans les tables sont données diverses indications à propos de température :
- Température maximum d’utilisation en continu
- Température limite avant déformation
- Perte de poids selon l’usage
Température maximale d’utilisation
Elle est définie comme celle qui entraîne une perte de poids de 2% par tranche de 24 heures. Pour de nombreuses applications cette limite est envisageable pratiquement ; il n’est pas possible de la dépasser au-delà de quelques jours sans voir la résine subir des dommages. Dureté et pouvoir adhésif sont nettement réduits à l’approche de cette limite. Si la résine doit rester stable pendant un an, et conserver toutes ses propriétés, on abaissera cette limite de 20 à 80°C.
Température limite avant déformation
Cette limite est inférieure à la précédente. Elle donne un point de repère afin d’anticiper la déformation mécanique de la résine.
Résistance à l'arrachement
Deux plaquettes collées l’une à l’autre sont soumises à une traction parallèle à leurs plans, jusqu’à rupture de l’assemblage.
On nomme « résistance à l’arrachement » la valeur maximale de la force en fonction de l’épaisseur du collage. Elle est donnée en différentes unités PSI (pounds per square inch), N/cm², kPa/cm² (kilopascal), etc…
Ces unités se correspondent ainsi :
- 1 PSI = 0,6894 N/cm² = 0,00703 kPa/cm²
- 1 MPa = 10² N/cm²
Rétention aqueuse
La résistance à l’humidité est une mesure du potentiel de la résine polymérisée à capturer l’eau. On mesure la variation de poids de la résine immergée directement dans l’eau pendant une durée donnée à une température constante ; cette valeur est donnée en pourcentage de poids. Ceci permet de comparer le comportement des différents matériaux en présence d’humidité.
Consistance
La consistance des époxydes actuellement disponibles va du liquide au solide (de forme stable, très visqueux, thixotrope). Les résines non « chargées » sont bien caractérisées par une mesure de leur viscosité, qui donne en millipascals.secondes (mPa.s) ou en centipoises (cps)- leur tendance à l’écoulement.
Par exemple
- Eau...................... 1,7 mPa.s
- Glycérine ............ 1499 à 1700 mPa.s
- Huile.................... 300 à 3000 mPa.s
- Époxyde.............. 100 à 4000 mPa.s
Dans le cas des résines chargées cette indication est un peu plus délicate ; la charge augmente ou diminue la thixotropie : il s’agit de produits pâteux. Ces produits thixotropes sont caractérisés par leur état « de forme stable » au repos qui peut être transformé par des sollicitations mécaniques (mouvements, diminution de volume) en un état visqueux proche de l’écoulement.
Des exemples de tels comportements sont donnés par le beurre tendre ou par la crème glacée ; ils sont de forme stable au repos mais s’écoulent de manière limitée lorsque, par exemple, on les manipule à la cuiller. On décrit donc mieux la consistance des résines chargées par une échelle du type : pâteuse, mais peut s’écouler, thixotrope, fortement thixotrope, thixotrope pâteux, etc… La donnée d’une mesure de viscosité ne renseigne en général pas plus avant.
Le rôle de la « charge »
Les résines avec et sans charges présentent des différences fondamentales.
Résines conductrices de la chaleur
Leur charge peut être : de l’oxyde d’aluminium, de l’argent, du nickel ou de l’aluminium. Celle-ci représente entre 60% et 75% du poids de la résine. Les plus utilisées sont chargées à l’alumine (oxyde d’aluminium). En effet, le métal utilisé comme charge dans les autres produits leur confère une meilleure conductibilité thermique, mais leur fait perdre le caractère d’isolant électrique.
C’est souvent la valeur obtenue pour la résistance à la chaleur au contact entre la résine et les pièces à assembler qui guide le choix de la conductivité thermique de celle-ci. Il est donc plus adéquat et pratique de comparer les résistances à la chaleur de l’ensemble des composants que de jouer sur la seule conductivité thermique de l’époxy.
Résines sans charge ajoutée
Elles ont un grand nombre d’applications, en particulier les collages de verres, de fibres optiques, etc…
Indice de réfraction
Pour la majorité d’entre elles, il se situe aux alentours de n = 1,5. Un type spécial permet d’obtenir n = 1,4. Cet indice comparativement plus faible que la colle permet d’obtenir des réflexions totales là où le plastique se détériorerait ou ne pourrait pas être employé.
Rétraction
Ces colles se rétractent à la chaleur. Cette perte de volume peut induire des tensions, voire dans les cas plus graves des déchirures. L’intensité des tensions dépend essentiellement du type de résine utilisé. Il est souhaitable que celle-ci ne contienne aucun solvant. En effet si aucun solvant n’affecte la résine pendant son durcissement, la rétraction est faible (moins de 1%). Pour des couches très minces, on assiste parfois à un écaillage total lors de la polymérisation.
Techniques d'utilisation
La consistance la plus fréquente rencontrée en utilisation industrielle est celle d’une pâte thixotrope. Dans la réalisation de structures plus fines on utilise des résines liquides. Les principales techniques d’utilisation sont les suivantes :
Sérigraphie
Une raclette fait passer la résine au travers d’un tamis de nylon ou d’acier. Le tamis comporte un écran sur sa face inférieure, qui agit comme un pochoir afin que les grains de résine passant à travers le tamis n’occupent que les emplacements libres. Le substrat se trouve de 0,5 à 1 mm sous le tamis. Lorsque l’on tire la raclette, le tamis vient le toucher et l’époxyde s’y dépose. On utilise pour les résines «chargées» des tamis comportant entre 180 et 325 mailles par pouce (soit entre 70 et 128 mailles par cm) choisis en fonction de la granulométrie de l’époxyde employée. Dans la mesure où l’absence de solvant ainsi que le temps de pottage sont respectés, la durée de réalisation d’un assemblage par cette technique peut atteindre plusieurs jours (elle varie bien sûr suivant la résine utilisée). Cette technique est excellente pour le collage précis de surfaces planes en production de masse.
Tamponnage
Il faut préparer une fine couche de résine (épaisseur de 200 à 300 µm). En appliquant dessus un tampon métallique environ la moitié de l’époxyde (100 à 150 µm) est prélevée. Après dépose sur le support à coller il ne reste qu’une couche de 50 à 75 µm. La seconde pièce de l’assemblage prévu peut alors être appliquée avec la pression requise sur le point de colle préparé. La colle est ainsi appliquée en plusieurs points séparés afin de former un réseau d’assemblage des pièces. En réglant la dimension du tampon en fonction des formes des dites pièces, on obtiendra un collage parfait, même des pièces anguleuses. Cette technique extrêmement précise permet d’espérer des cadences de production, même manuellement, de 600 à 800 pièces à l’heure. Des préparations existent, qui sont spécialement étudiées pour cette technique quant à leur thixotropie et leur viscosité. Il est en outre essentiel qu’aucun filament ne se forme par étirement lorsque le tampon est éloigné de la résine.
Dosage sous pression d’air
Pour cette procédure on utilise une très petite quantité de colle (par exemple 5 cm3) placée dans une cartouche. Cette cartouche est équipée à son ouverture basse d’une pipette de dosage. Le volume, le débit et la pression sont assurés par un système d’air comprimé. Ce contrôle permet d’obtenir un dosage précis de la quantité de résine expulsée. On peut par cette méthode réaliser des dosages manuels ou automatisés.
Méthode à la spatule
Naturellement on peut aussi placer à la main la résine sur la surface à encoller à l’aide d’une petite spatule. Malgré son imprécision, cette méthode peut être utile pour la recherche de solutions, pour la production de toutes petites séries ou encore pour la réparation.
Centrifugation
Les pièces en forme de disque peuvent être enduites très régulièrement par centrifugation. Pour cela on maintient la pièce sur un cylindre rotatif grâce au vide et la résine est déposée sur le disque pendant que le cylindre tourne à grande vitesse. La force centrifuge étale le produit époxyde vers l’extérieur et réalise ainsi un film d’épaisseur très régulière à la surface.
Choix, préparation
Choix d'une résine
Il y a toujours de nombreux facteurs à prendre en compte lorsque l’on a à choisir un produit époxyde hautes performances pour une application particulière. Deux éléments fondamentaux doivent être envisagés dès le départ de cette réflexion :
-
Quelle technique pourra être utilisée lors de la mise en production réelle ? Lesquelles sont inenvisageables au contraire ? Quel est la cadence de travail permise par la résine ? A quelle température maximale les autres pièces peuvent être portées lors du processus de polymérisation ?
-
À quelles spécifications particulières la résine polymérisée doit-elle répondre dans l’utilisation prévue ?
La réponse à la première question conduit aux quantités à commander et à stocker. Mais la méthode de mise en œuvre et l’organisation du travail dictent le choix de la consistance, de la viscosité et peut-être même du cycle de polymérisation.
Les spécifications identifiées par la réponse à la seconde question conduisent aux choix de paramètres comme :
- Quelle conductivité (thermique, électrique) ?
- Quelle température maximale d’usage ?
- Quelles résistances mécanique ?
- Quelle résistance à l’humidité ?
- Quelle résistance aux chocs thermiques ?
- Quelle résistance aux cycles de température ?
- Quelles qualités optiques ?
- Quels matériaux en contact ?
- Quel cahier de charges (NASA, etc...) ?
Comme chaque cas est un cas d’espèce, le choix final est souvent un compromis entre toutes ces exigences.
Nous sommes à votre disposition pour vous assister et vous apporter notre expertise.
Précautions, préparation
Stockage
La température doit rester comprise entre 20° et 25°C. Il faut assurer la fermeture permanente des emballages, afin de conserver intactes les composants volatils des produits. Dans ces conditions les temps de conservation annoncés seront respectés. La plupart pourront pourtant être conservés nettement plus longtemps. La perte de qualité acceptable est déterminée par l’état de la résine : la règle générale est qu’une résine est en bon état aussi longtemps qu’elle se laisse travailler.
Dans le cas d’un produit à un seul composant, le temps habituel de 6 mois peut être considérablement allongé si on le stocke au réfrigérateur (2 à 7°C). On pensera à le sortir au moins une journée avant son usage, sans ouvrir son emballage pour autant. Il faut porter alors une grande attention à la condensation sur le couvercle, qui pourrait conduire à la destruction de l’époxyde.
Préparation de la résine
L’époxyde doit être malaxé avec application. S’il y a deux composants, nous conseillons de mélanger individuellement chacun de ces composants. Il convient de porter attention à ce que ni cette agitation préalable, ni le mélange n’introduisent trop de bulles d’air, aussi petites soient-elles.
Un réchauffement de la résine jusqu’à 35 à 50°C réduit notablement sa viscosité (elle se comporte alors comme une huile moteur), ce qui peut faciliter malaxage et mélange. On gardera présent à l’esprit le fait qu’une telle pratique réduit le temps de pottage, et qu’il faut donc dans ce cas travailler rapidement.
Préparation des surfaces
Tous résidus de colle, toutes poussières, toutes traces d’huiles, de graisses, toutes salissures doivent être supprimées de la surface avant encollage. Pour l’huile et la graisse, de bons résultats sont obtenus avec les solvants organiques comme l’acétone, l’éthanol, le MEC (Méthyléthylcétone).
Ce nettoyage de la surface améliore l’adhésion de la résine. Celle-ci adhère généralement bien aux métaux (à l’exception du chrome et du titane), au verre, aux céramiques et matières synthétiques. Parmi ces dernières il peut être nécessaire, pour les polyoléfines ou les matériaux à base de PTFE de prévoir une imprégnation préalable. On peut utiliser par exemple un mélange d’oxygène et d’hexafluorure de soufre.
Polymérisation
Elle doit être conduite en suivant les indications figurant sur l’emballage. Plus on aura de temps pour la polymérisation, meilleur sera le résultat. On peut d’ailleurs améliorer ce pouvoir adhésif et la stabilité du produit, en procédant à une consolidation par chauffage, par exemple 4 heures à 90°-120°C. La résistance aux fluides du produit final dépend fortement de cette température de polymérisation.
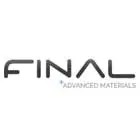
Duralco® 132 Adhésif époxy
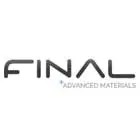
Duralco® 133 Adhésif époxy
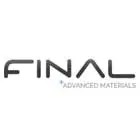
Duralco® 134 graisse thermique
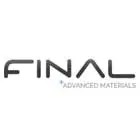
Duralco® 135 graisse thermique
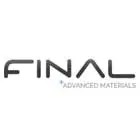