Elektrisch leitfähiges Epoxidharz von Cotronics
Vorstellung von elektrisch leitfähigen Epoxidharzen
Durch die Kombination von exklusiven Cotronics® Harzen und Härtern mit speziellen Füllstoffen haben wir die für bestimmte Anwendungen erforderliche elektrische Leitfähigkeit erreicht. Diese Klebstoffe haften auf Glas, Keramik, Metallen und Kunststoffen. Sie besitzen eine ausgezeichnete Beständigkeit gegenüber Chemikalien und Lösungsmitteln.
Die leitfähigen Schichten, die mit diesen Produkten erzeugt werden, können in der Elektronik Lötstellen ersetzen, Transistoren fixieren, Platinen reparieren, Leiterbahnen bilden usw. Ihre Aushärtung kann bei 120 °C und mehr beschleunigt werden.
- Duralco® 120: Seine Formel garantiert eine volle Haftung bei Temperaturen von -30 °C bis +250 °C im Dauerbetrieb und bei Spitzentemperaturen von 260 °C mit Unterbrechungen. Der Füllstoff ist ein aktives, ultrafein gesiebtes Silberpulver, das eine optimale elektrische Leitfähigkeit gewährleistet. Es polymerisiert bei Raumtemperatur. Eine leichte Erhöhung der Temperatur beschleunigt den Aushärtungsprozess. Dieser Kleber haftet perfekt auf Kupfer, Stahl, Aluminium, Blei, Glas, Keramik, Kunststoffen und anderen Materialien.
- Die leitfähigen Schichten, die mit diesem Harz erzeugt werden, können wirksam Lötstellen auf Komponenten und elektronischen Schaltungen ersetzen, Transistoren fixieren, Platinen reparieren oder Leiterbahnen bilden.
- Duralco® 122: Kostengünstigeres Harz mit einem Füllstoff aus Nickel. Polymerisiert bei Raumtemperatur und ist hitzebeständig bis 260 °C.
- Duralco® 124: Mit Silberfüllstoff, verfügt über die Leistungsstärke des besten anorganischen Cotronics-Harzes. Polymerisiert bei Raumtemperatur und ist hitzebeständig bis 340 °C.
- Duralco® 125: Flexibles Harz mit Silberfüllstoff. Polymerisiert bei Raumtemperatur und ist hitzebeständig bis 230 °C.
- Duralco® 127: Dieses Harz mit Graphitfüllstoff ist das günstigste. Polymerisiert bei Raumtemperatur und ist hitzebeständig bis 200 °C.
Technische Daten der elektrisch leitfähigen Epoxidharze
Ratschläge für die Verarbeitung der hochtemperaturbeständigen Epoxidharze.
Cotronics®-Epoxide im Allgemeinen
Diese hochleistungsfähigen Spezialprodukte werden nach gemeinsamen Methoden auf Basis allgemeiner Prinzipien spezifiziert und hergestellt, aus denen sich ihre Ähnlichkeiten ergeben; sie unterscheiden sich voneinander durch:
- die Anzahl der Komponenten (1 oder 2)
- etwaige zusätzliche Füllstoffe
- ihre Polymerisation, bei Raumtemperatur oder durch Vorwärmen (bis zu 120 °C)
Ein bisschen Chemie
Epoxidharze sind Mischungen aus organischen Stoffen, meist Oligomere, die mehr als eine Epoxidgruppe pro Molekül enthalten. In den Cotronics®, Duralco® und Durapot® Produkten wird Novalac-Harz verarbeitet; dieses wird durch Kondensationsreaktionen in saurem Milieu (wodurch sie katalysiert werden) zwischen Phenol- oder Kresolradikalen einerseits und Formaldehyd andererseits gehärtet.
Als Härter verwenden wir:
- Amine für Systeme, die bei Raumtemperatur polymerisieren
- Säureanhydride für Systeme, die bei höheren Temperaturen polymerisieren
- BF3-Amin-Komplex für Ein-Komponenten-Systeme
Bei der chemischen Aushärtung entsteht durch die Polymerisationsreaktionen eine Verbindung, die durch ihre dreidimensionale Molekularstruktur unschmelzbar und unlöslich wird.
Da sich diese Reaktionen stöchiometrisch verhalten, ist es für die Qualität des Ergebnisses entscheidend, dass die Mischungsverhältnisse exakt eingehalten werden. Durch die Verwendung von Füllstoffen lassen sich bestimmte Eigenschaften wie die thermische oder elektrische Leitfähigkeit oder die mechanische Festigkeit verändern. Ein Füllstoff wie Silber (Duralco® 118, 120, 124) ermöglicht elektrisch leitende Verbindungen, während ein Füllstoff aus Aluminiumoxid (Duralco® 4400, 4700) wärmeleitenden Verklebungen schafft, die sich jedoch wie elektrische Isolatoren verhalten.
Ein- und Zweikomponenten
Zweikomponentenharze haben eine bessere Haltbarkeit bei Raumtemperatur; sie besitzen generell bessere mechanische Eigenschaften und bieten eine große Bandbreite an thermischen Eigenschaften und anderen physikalischen Parametern.
Der Hauptvorteil eines Einkomponentensystems besteht darin, es nicht unter Beachtung eines exakten Mischungsverhältnisses anmischen zu müssen; andererseits verändert sich die Konsistenz solcher Systeme (Viskosität, Thixotropie) während der Lagerung bei Raumtemperatur langsam.
Topfzeit
Mit diesem Begriff bezeichnet man die Zeit, in der ein Zweikomponentenprodukt nach dem Anmischen verarbeitet werden kann (oder ein Einkomponentenprodukt aufgetaut werden kann), ohne dass seine Verarbeitungsfähigkeit beeinträchtigt wird.
Lagerung
Die Produkte sollten bei 20 °C bis 25 °C gelagert und die Verpackungen stets sorgfältig verschlossen werden, um die Qualität zu erhalten. So bleiben die angegebenen Haltbarkeiten zuverlässig, oft sind die Produkte jedoch deutlich länger verwendbar. Entscheidend ist der Zustand des Harzes: Ein Harz ist so lange verwendbar, wie es sich gut verarbeiten lässt.
Erhitzen
Öffnen Sie die Patronen, bevor Sie sie auf Raumtemperatur bringen. Kondenswasser muss von den Öffnungen ferngehalten werden. Das Harz danach auf keinen Fall wieder kühlen!
Beispiel
Zum Auftauen einer Patrone mit 3 cm³ Harz mit Silberfüllstoff H20E. Von -40 °C bis 20 °C mit warmer Luft bei 25 °C, 20 Minuten Auftauen, 200 % Sicherheit: 1 Stunde.
Auslieferung
Die Kälte wird durch einen Transport auf Trockeneis (-78 °C) gewährleistet. Beim Empfang muss noch mindestens ein Kilogramm Trockeneis vorhanden sein. Harz und Trockeneis sind mit Isolierhandschuhen zu handhaben; direkter Kontakt mit Wasser oder anderen Lösungsmitteln könnte das Harz zerstören.
Reinigung
Die Reinigung von Werkzeugen, die mit nicht ausgehärtetem Harz verunreinigt sind, erfolgt mit:
- Aceton
- MEC (Methylethylketon)
Ausgehärtete Verunreinigungen lassen sich mit Hitze, starkem Reiben oder einem Epoxid-Entferner (z. B. Dichlormethan) entfernen.
Eigenschaft der Oberflächen
Die Anwendungsflächen müssen frei von Verunreinigungen, Staub, Öl oder Lösungsmittelresten sein, um eine optimale Verklebung zu gewährleisten.
Polymerisationszyklus, Aushärtung
Der Aushärtungszyklus besteht aus einer Reihe von Temperaturstufen, die ein Harz durchlaufen muss, damit es korrekt polymerisiert. Für jedes Produkt sind mehrere Kombinationen von Temperaturkurven bzw. Haltezeiten möglich, wodurch sie für verschiedene Anwendungen einsetzbar sind.
Temperaturspannen
Epoxid- und Polyamidharze sind organische Gemische, die sich bei hohen Temperaturen zersetzen und verdampfen.
Maximale Anwendungstemperatur
Das ist die Temperatur, die zu einem Gewichtsverlust von 2 % pro 24 Stunden führt. Für viele Anwendungen ist diese Grenze praktisch vorstellbar; es ist nicht möglich, sie länger als einige Tage zu überschreiten, ohne dass das Harz Schaden nimmt. Härte und Klebkraft werden bei Annäherung an dieses Limit deutlich reduziert. Wenn das Harz ein Jahr lang unter Beibehaltung all seiner Eigenschaften stabil bleiben soll, muss dieses Limit um 20-80 °C gesenkt werden.
Grenztemperatur vor Verformung
Dieses Limit ist niedriger als das vorherige. Es dient als Anhaltspunkt, um die mechanische Verformung des Harzes frühzeitig zu vermeiden.
Reißfestigkeit
Zwei miteinander verklebte Pads werden einer Zugspannung parallel zu ihren Ebenen ausgesetzt, bis die Verbindung reißt.
Flüssigkeitsretention
Die Feuchtigkeitsbeständigkeit ist ein Maß für das Potenzial des ausgehärteten Harzes, Wasser zu binden. Man misst die Gewichtsänderung des Harzes, das für eine bestimmte Zeit bei einer konstanten Temperatur direkt in Wasser eingetaucht wird; dieser Wert wird in Gewichtsprozent angegeben.
Konsistenz
Die Konsistenz der gegenwärtig erhältlichen Epoxiden variiert von flüssig bis fest (formstabil, hochviskos oder thixotrop). Harze ohne Füllstoffe lassen sich gut durch eine Messung ihrer Viskosität charakterisieren, die ihre Fließneigung in Millipascal.Sekunden (mPa.s) oder Centipoise (cps)- angibt.
Die Rolle des „Füllstoffs“
Harze mit und ohne Füllstoffe weisen grundlegende Unterschiede auf.
Wärmeleitende Harze
Als Füllstoff können Aluminiumoxid, Silber, Nickel oder Aluminium verwendet werden. Der Füllstoff macht zwischen. 60 und 75 % des Harzgewichts aus. Die meistverwendeten Harze haben Aluminiumoxid als Füllstoff.
Ungefüllte Harze
Sie haben ein breites Anwendungsspektrum, insbesondere für die Verklebung von Glas, Lichtwellenleitern usw.
Brechungsindex
Bei den meisten Harzen liegt der Brechungsindex bei etwa n = 1,5. Mit einem Spezialtyp kann man einen Wert n = 1,4 erreichen.
Schwindung
Diese Klebstoffe schrumpfen bei Hitze. Dieser Volumenverlust kann zu Spannungen und in schweren Fällen sogar zu Rissen führen.
Verwendungstechniken
Die in der Industrie am häufigsten verwendete Konsistenz ist die thixotrope Paste. Bei der Herstellung feinerer Strukturen werden flüssige Harze verwendet.
Siebdruck
Ein Rakel drückt das Harz durch ein Nylon- oder Stahlsieb. Das Sieb hat an seiner Unterseite eine Siebmaske, die wie eine Schablone fungiert.
Stempelverfahren
Zunächst muss eine dünne Harzschicht vorbereitet werden (Dicke 200 bis 300 µm). Durch das Aufbringen eines Metallstempels auf dieser Schicht wird etwa die Hälfte des Epoxids entfernt.
Dispensen
Für dieses Verfahren wird eine sehr kleine Menge Klebstoff (z. B. 5 cm³) verwendet, der sich in einer Patrone befindet.
Auftrag mit dem Spatel
Natürlich kann man das Harz auch von Hand mit einem kleinen Spatel auf der zu verklebenden Fläche auftragen.
Zentrifugieren
Scheibenförmige Teile können durch Zentrifugieren sehr gleichmäßig beschichtet werden.
Auswahl, Zubereitung
Wahl eines Harzes
Bei der Wahl eines Hochleistungs-Epoxidharzprodukts für eine bestimmte Anwendung sind immer eine Vielzahl von Faktoren zu berücksichtigen.
Vorsichtsmaßnahmen, Zubereitung
Lagerung
Die Temperatur muss zwischen 20 °C und 25 °C bleiben. Es muss sichergestellt werden, dass die Verpackungen dauerhaft verschlossen sind.
Zubereitung des Harzes
Das Epoxidharz muss gründlich angemischt werden. Bei zwei Komponenten wird empfohlen, jede Komponente zunächst einzeln zu verrühren.
Vorbereitung der Oberflächen
Vor dem Verkleben müssen alle Kleberreste, Staub, Öl, Fett und Schmutz von der zu verklebenden Oberfläche entfernt werden.
Polymerisation
Sie sollte nach den Anweisungen auf der Verpackung geführt werden.
Lösen einer Klebeverbindung und Reparatur
Eine Klebeverbindung kann auf vielerlei Arten gelöst werden:
Reinigung
Nicht polymerisierte Rückstände lassen sich leicht mit Lösungsmitteln entfernen; ist das Harz bereits polymerisiert, auch nur teilweise, sind chlorhaltige Lösungsmittel wie Dichlormethan zu verwenden.
Sicherheit
Die gesetzlichen Sicherheitshinweise und Vorschriften sind in den Sicherheitsdatenblättern enthalten. Auf jeden Fall sollte man den Hautkontakt vermeiden und vor allem ständig Handschuhe tragen.
Final Advanced Materials verfügt über ein umfassendes Sortiment an Epoxidklebstoffen. Sie sind elektrische Leiter, die Temperaturen bis zu 300 °C standhalten.
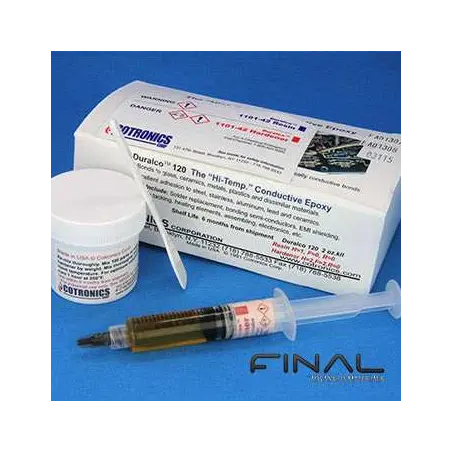
Duralco® 120 Epoxidklebstoff
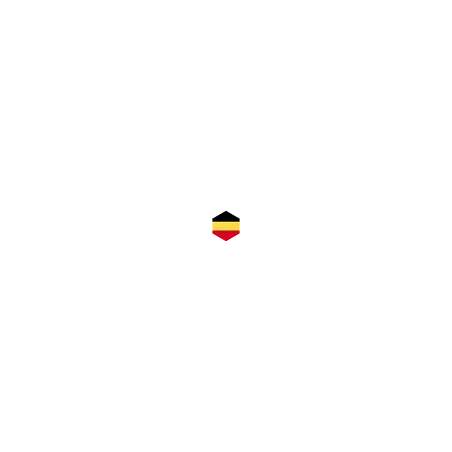
Duralco® 122 Epoxidklebstoff
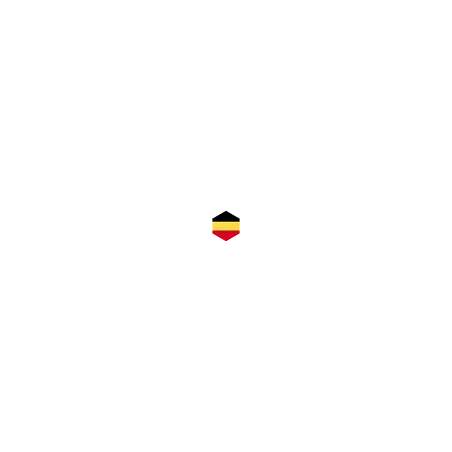
Duralco® 124 Epoxidklebstoff
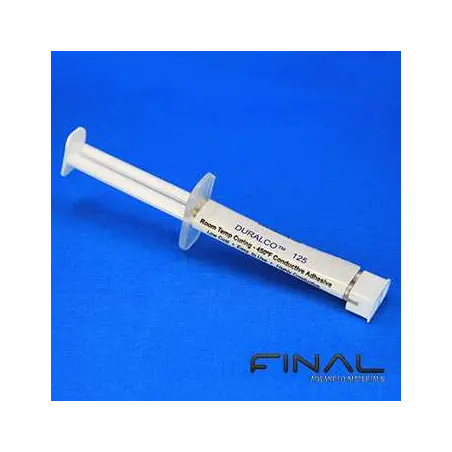
Duralco® 125 Epoxidklebstoff
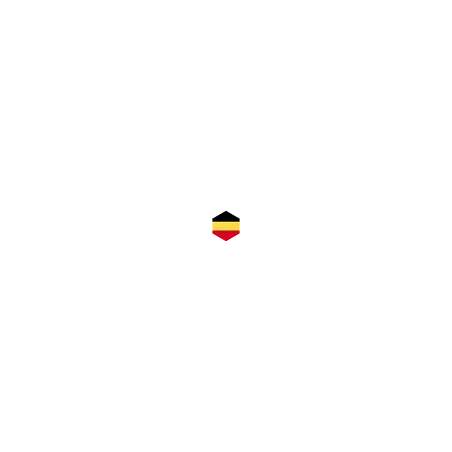