Composite Materials
Overview: Composite Materials
Final Advanced Materials formulates, processes, and manufactures a wide range of composite materials with high heat capacity. The proposed solutions are based on quality materials, machinable with conventional tools, available in all general mechanical workshops. Our team accompanies you from the selection of the material to the assembly of the finished product.
Technical composites originate from two sources:
- Composites based upon organic resins
- Mineral composites
Technical composites permit the engineering of refractory products for targeted applications:
Thermally-insulating mechanical components
- Glass-making industry, smelting works, mechanical construction,
- Aluminium industry, steel making,
- Construction of furnaces, nuclear industry, etc.
Thermal insulation panels
- Particle board presses,
- Vulcanizing presses,
- Plywood presses, stamping presses,
- Moulding presses, injection-moulding presses,
- Injection-moulding tools, etc.
Furnace claddings and components
- Electric furnaces, induction furnaces, arc furnaces, crucible furnaces, etc.
Applications of Composite Materials
Organic resin-based composites permit the production of components which remain dimensionally stable at temperatures up to 500 °C. Mineral composites (with inorganic bonds) provide options for a wide range of applications at higher temperatures, from 500 up to 2,000 °C.
There are numerous fields of application for these materials: they are extensively employed in the electrical, chemical, nuclear, glass-making and aluminium industries, in mechanical construction, furnace construction and steel making.
Thermally-insulating mechanical components
Standard panels provide the option for the off-plan machining of complex components. The choice of composite material is dependent upon the thermal and mechanical loads involved. These constraints will dictate the type of composite, its thermal insulation capabilities and mechanical resistance, in the interests of perfect adaptation to its final application.
Final Advanced Materials machines various types of products: one-off components, prototypes and series production components.
Examples of mechanical components produced from refractory composites:
- Static electrical insulators in electric power installations
- Electrical insulators in induction systems
- Construction of electric furnaces, induction furnaces and arc furnaces
- Flat gaskets and sealing components
- High-frequency welding technology
- Insulation of press plates
- High-voltage switchgear
- Heating elements
Thermal insulation panels
Thermal insulation panels produced from technical composites provide the ideal physical and chemical compromise for thermal insulation. Thermal insulation panels act as insulating barriers for the effective protection of sensitive components, particularly hydraulic, electrical and electronic circuits. This type of product is very closely tailored to the requirements of manufacturers of injection-moulding presses. Thermal insulation panels also permit the even distribution of heat and the effective control of thermal masses. They thus permit the achievement of substantial energy savings and the execution of rational production. The product qualities of E-6000, E-60 and MC-5000HT have been developed, not only to ensure high-temperature resistance but also to deliver excellent mechanical strength and exceptional ease of machining.
Examples of applications of thermal insulation panels:
- Vulcanizing presses, plywood presses, stamping presses, injection-moulding presses, moulding presses, etc.
Furnace claddings and components
Mineral-based technical composites provide an effective solution for the insulation of industrial furnaces, where they are incorporated in a mechanical assembly. They are advocated by health and safety standards for refractory fibre-based flexible insulating materials.
Technical composite panels are available in large dimensions and are simple to deploy, using techniques which are closely akin to traditional joinery. After installation, their properties remain consistent, even in response to substantial thermal loading, and with no release of harmful dusts.
Examples of applications of furnace components:
- Electric furnaces, induction furnaces, arc furnaces, crucible furnaces, etc.
Benefits of Composite Materials
- Thermal resistance
- Excellent dimensional stability
- Suitability for sealing applications
- Exceptional toughness
- Excellent resistance to radiation
- Good mechanical resistance
- High dielectric strength
- Substantial wear resistance
- High compressive strength
- Limited release of gases
Composite Materials Products
Final Advanced Materials works with various types of technical composites. Materials may have organic or mineral bonds, depending upon their application. Mineral technical composites are resistant to higher temperatures than organic technical composites.
Organic Technical Composites, up to 500 °C
Our range of technical composites based on fibreglass and epoxy resin allows us to offer you a complete selection of solutions up to a maximum temperature of 350 °C. These technical composites offer full thermal and electrical insulation. In addition to controlled flammability, they offer arc protection and can be used wherever temperature resistance, dimensional stability and mechanical resistance are essential parameters. Furthermore, we have endeavoured to make not only strong materials, but also excellent workability in order to guarantee easy mechanical work with conventional tools.
Epoxy Resins, up to 350 °C
Epoxy, or polyepoxide, is a resin produced by the polymerization of epoxide monomers using a hardener. Hardening is achieved by the action of heat. This material is frequently employed in the form of a composite adhesive or paint.
- E-6000 : This product combines low thermal conductivity (0.25 W.m-1. K-1) with low density, thus permitting the production of more delicate and lightweight insulating components. It is resistant to a continuous temperature of 220 °C and a peak temperature of 320 °C. This material is laminated from a basis of glass-fibre matting and whitish-yellow epoxy resin. It shows good resistance to chemical agents.
- E-60 : This product delivers a superior mechanical and thermal performance to E-6000 but is less effective as a thermal insulator. It is resistant to a continuous temperature of 260 °C and a peak temperature of 330 °C. It is laminated from a basis of grey-coloured glass roving and epoxy resin.
MC5000-HT Mica-Silicone, up to 700 °C
Mica is a mineral which is primarily comprised of aluminium silicate and potassium. It is characterized by its laminated structure, which is typical of phyllosilicates, its metallic lustre and its high resistance to heat. The properties and uniform qualities of micas make them ideal candidates for thermal insulation applications. Mica-based products deliver high mechanical strength and high compressive resistance, even at high temperatures. They show exceptional resistance to flames, arcing and electrical erosion. MC5000-HT mica is comprised of 90 % phlogopite mica and 10 % silicone binder. It is resistant to a continuous temperature of 700 °C. Mica panels can be used as a replacement for products containing asbestos.
Important: it is necessary for MC5000-HT to be compressed between two plates or flanges. Mechanical compression prevents any crumbling of the product in response to the action of temperature, given that the silicone binder deteriorates at temperatures in excess of 300 °C, and replacement of the component will therefore be necessary after dismantling.
Mineral-Bonded Products, for applications in excess of 500 °C
Our range of mineral-bonded technical composites incorporates various materials, for the optimum response to issues arising in the field. These products are resistant up to a maximum temperature of 2,000 °C.
The temperature resistance of a material is generally inversely proportional to its density, its mechanical strength and its machinability.
Calcium Silicate, up to 1,000 °C
Calcium silicate is a powder with the formula Ca2SiO4. This product is essentially employed for its excellent high-temperature properties. In block form, calcium silicate can easily be cut, chiselled, drilled, screwed and machined using specialized equipment, or even using conventional joinery tools and techniques. Any cutting installation must incorporate a dust extraction facility. Calcium silicate is a low density material, white in colour. It has no odour or taste, and poses no known health risks. Its derivatives are highly valued for their low thermal conductivity, their high resistance to heat and their limited dimensional shrinkage.
Nano-T Ultra Nanoporous Silica, up to 1,050 °C
Nanoporous silica originates from applied research in ceramic nanostructures. This is an exceptionally lightweight insulating product, with an extremely low coefficient of thermal conduction. It is primarily comprised of silica, to which opacifying agents are added for the minimization of infrared radiation. Nanoporous silica is non-combustible and is graded A1 in the Euroclass European fire performance rating. It is insensitive to thermal impacts. It must be protected against liquids, which may destroy its nanoporous structure. It is possible to protect this material using various types of packaging, in the interests of facilitating its use and conservation. For example, PE film or aluminium foils may be employed. This packaging also protects the product against mould.
ZYZ and ZYC Zirconium Oxide Fibre, up to 1.700 °C
Zirconium Oxide Boards Type ZYZ and ZYC are rigid, refractory structures composed of yttria stabilized zirconia fibres that are bonded with silica. This unique composition provides ZYZ insulation with the low thermal conductivity of zirconia fibres combined with the strength and machinability of a silica bonded material. ZYZ is evenly bonded, allowing it to be machined to tight tolerances and intricate shapes.
SIZAL®, up to 1,800 °C
SIZAL®CELL is a range of non-fibrous insulation products manufactured from alumina microspheres. Ultra-light, SIZAL®CELL is designed for high-temperature applications up to 1,800 °C.
SIZAL®BOARD is a range of rigid high-temperature insulation. These products are made of silica and alumina, bonded by an inorganic binder. All SIZAL®BOARD products can be delivered pre-calcined. Cooking parts at more than 350 °C eliminates all traces of organic binders that may be present in the materials. This operation avoids gas emissions and potential pollution during more sensitive applications.
ZYBF and FBD Zirconium Oxide Fibre, up to 2,200 °C
ZYBF and FBD fibres are the result of the Zircar Process which transforms an organic fibre into a ceramic one. The new fibre usually has a diameter of 6 to 10 μm and a serrated outer surface. All zirconia bulk fibres are made of nearly 100 % zirconia phase stabilized with 10 % yttria. The yttria stabilizes the tetragonal / cubic structure by preventing the monoclinic to tetragonal crystal transformation that occurs at 1,170 °C in pure un-stabilized or insufficiently stabilized zirconia. This undesirable transformation causes an 11 % volume change in the crystal unit cell size that can cause micro-cracking and reduced physical strength in the bulk solid.
- ZYFB : Yttria stabilized zirconia is an electrical semiconductor at elevated temperatures. This conductivity arises from the different valences of ionic Zr4+ and Y3+. Electricity is conducted at elevated temperatures (700-800 °C) as oxygen ions are induced to flow through the stabilized zirconia structure. This phenomenon forms the basis of zirconia oxygen sensors.
- FBD : They have extremely high stability for use as high as 2,000 °C and can be exposed to significantly higher temperatures, depending on the application. It has good hot strength up to 1,700 °C, and can used as protection sleeve, insulation for industrial furnaces or setter for loads up to twice its weight. This product can be machined with conventional tooling.
Machinable zirconium fibre technical composites are available in the form of panels, disks or tubes, in three different densities.
Physical variables included in this documentation are provided by way of indication only and do not, under any circumstances, constitute a contractual undertaking. Please contact our technical service if you require any additional information.
Calcium silicate composite
FBD Zirconium Oxide Composite
Glass-Epoxy Composite
Mica-Silicone Composite
Nanoporous Silica Nano-T Composite
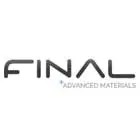
Sizal® Board Composite
SIZAL® CELL - Composite for insulation
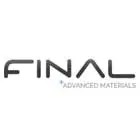
ZYC and ZYZ Zirconium Oxide Composites
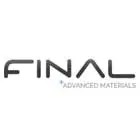